“It’s Only Fabric.”
This one statement made my head spin … made me see red … put me at a loss for words. You get the idea.
Yes, I heard this from a cutting room manager (you are reading that correctly) at a company I once worked at.
And here is the reason this statement was made ( I still shake my head when I think about it). We were discussing fabric flaws that were making their way to the shop floor and the need to do a better job of inspecting the fabric, and the pros and cons of inspecting upon receipt verses prior to release to cutting. We were inspecting goods when they were being released to cutting. This worked fine when there was enough lead time, but if we were running behind schedule some liberties were taken.
Recuts (cutting a replacement for the damaged component) were having an impact on productivity and lot completion. The shop was spending additional labor and money on handling garments twice and rushing the recut through production in order to get them back into their bundles.
Just as a reference, piece goods can make up anywhere from 60 to 70 percent of your products cost. There are several variables that come into play, such as the type of fabric being made, product being made, and the amount of SAM’s (time required to manufacture your product) required.
Now, remember that fabrics are selected months in advance of the manufacturing process. Fabric orders are based on projected sales, current trends and consumer tastes. Allowances are factored in on the fabric orders for waste. Whether they are defects in the fabrics or mistakes made in the manufacturing process.
Can you possibly anticipate every situation that will have a negative impact on your fabrics? Of course not. But you can plan and create processes and procedures that will reduce their impact on sales projections.
As I mentioned earlier, we had discussed the pros and cons of inspecting fabric upon receipt verses prior to release to cutting. I am a strong believer in touching things once. Receive the fabrics, inspect, identify any defects, clearly tag the defects, and store until needed. Sounds pretty straight forward. If excessive defects are found, the sales department can be alerted so they can notify customers if need be and modify their sales projections. The mill can be notified, and a credit can be requested if the defects are in excess of those stipulated in the sales agreement ( If defects exceed a certain percentage of the total purchase fabrics will be replaced or a credit will be applied to the invoice or to the next purchase).
I remember an instance at a men’s clothing company where I was employed. They had ordered a plaid fabric with a very prominent red thread running from selvage to selvage, and end to end. We had a very positive response from sales and had planned several large cuttings of sportscoats. However, as the fabric was being inspected, we found that red thread running through the fabric had slubs, flaws or were knotted.
I was paged to come to the 4th floor, where our piece goods and trims were stored. As I got off the elevator, I could hear Al the supervisor for the trim room yelling “Johnny, are you sure all these rolls are bad? Did you double check?” To which Johnny replied “Al, I’ve been look’n at fabric for 30 years. If I don’t know mistakes by now, I quit!” All joking aside, between Al and Johnny they had close to 80 years of piece good experience. I would stake my reputation on their recommendations; and had numerous times.
And for clarification these inspections were taking place upon receipt of goods, not issuance to the cutting room.
We determined that we could not salvage enough yardage to make a substantial cutting. We contacted the mill and they sent two employees to repair the defects by hand. These two ladies worked for three weeks unrolling, repairing and rerolling the fabric. This was the first, last and only time I heard of mill providing this type of service.
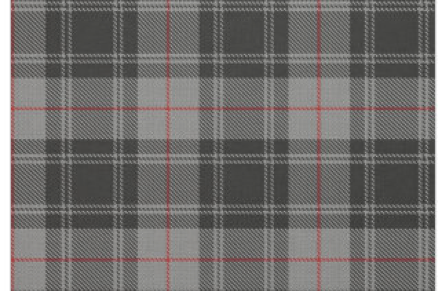
Plaid Fabric
Because we inspected upon receipt of goods, we were able to identify defects before the goods were issued to a cut, and set a plan into place.
As for the scenario I mentioned earlier (where the cutting room manager made the statement “it’s only fabric), we determined that inspection upon receipt was the best course of action. We created a SOP where we would inspect 10% all piece goods upon receipt from the mill, document each roll being inspected, recording actual yardage verses the mill tag, actual width verses mill width, mill lot and roll number, the inspectors name and date the roll was inspected.
We also created a process for inspection. Once a roll was started it had to be completed, regardless of how many defects were identified. Who ever started the roll must complete it. The yardage meter was zeroed out and the inspection began. The fabrics passed over the face of a back lit panel so that defects could be easily identified and marked. If a defect was found the inspector would retrieve a “swift tack gun” that had been loaded with plastic barbs and insert a plastic barb in the selvage adjacent to the point where the defect fell. This process went on for the entire roll. Once the roll was completed the ending yardage was recorded and the roll of fabric was either placed on a pallet to be moved for storage, or on the pallet for rolls with excessive defects.

Figure 1 Fabric Inspection Machine
Link for a demonstration video of a fabric inspection machine.

Figure 2 Swift Tack
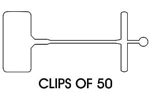
Figure 3 Barb
Link to product:

Figure 4 Front of ticket
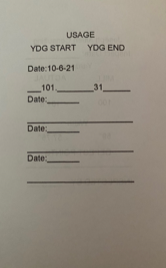
Figure 5 Back of ticket
Once this SOP was implemented, recuts reduced dramatically, bundle completion increased as did the factories efficiency.
Whether you are manufacturing in your own facility, or contracting to domestic or offshore manufacturing companies, establishing SOP, KPI’s and SLA’s for the inspection of your piece goods are critical.
Inquires for SOP's, KPI's and SLA's
That’s it for this edition. I hope you enjoyed reading it as much as I enjoyed writing it.
Until my next instalment, stay healthy and safe.
Comentarios